I finally got through the mile wide spreadhsheet that I told my buddy i would build for his surfboard factory management so I bought myself some guilt-free time to work on this beast.
The screen surround/bezel saga continues.
I'm still trying to figure out if there is some means to make what I have been learning with these bezel builds something others can use (because I can't just build these freaking things for anybody and ship them anywhere- unless somebody is cool with paying the probably $100+ it is at this point for the stupid transport) but I have zero skills or knowledge with digital stuff so I am at a loss.
Sorry-
So this thing still fit the cabinet properly but since it was only some thin MDF I knew it needed some support to live through what abuse it may endure- and it is going to effectively wind up finish as there will not be any screen covering plexi this in the cabinet- so it should look prettier than me at least.
And therefore like all meaningful crap in my life, it must be fiberglassed.
Conveniently, I have another 75 ft or so of 4oz cloth on my glass rack- so trimming a 30" piece is easy.
Cutting that to be a useful shape to accomodate the compound curves of this bezel monstrosity is not so bad for me at this point.

The last time I made one of these I actually used a factory built one as a mold to do this (and it was a huge pain in the ass) so this time I figured I would form my own foundation and go from there.
It is proving to be a hell of a lot easier than the previous path.
This is the paradigm going forward for sure.
Standard lamination activity at this point.
Polyester resin
Black pigment in this case
MEK as our lovely toxic polymerization oxidizing agent
Acetone for the mess I will inevitably make
Squeegee
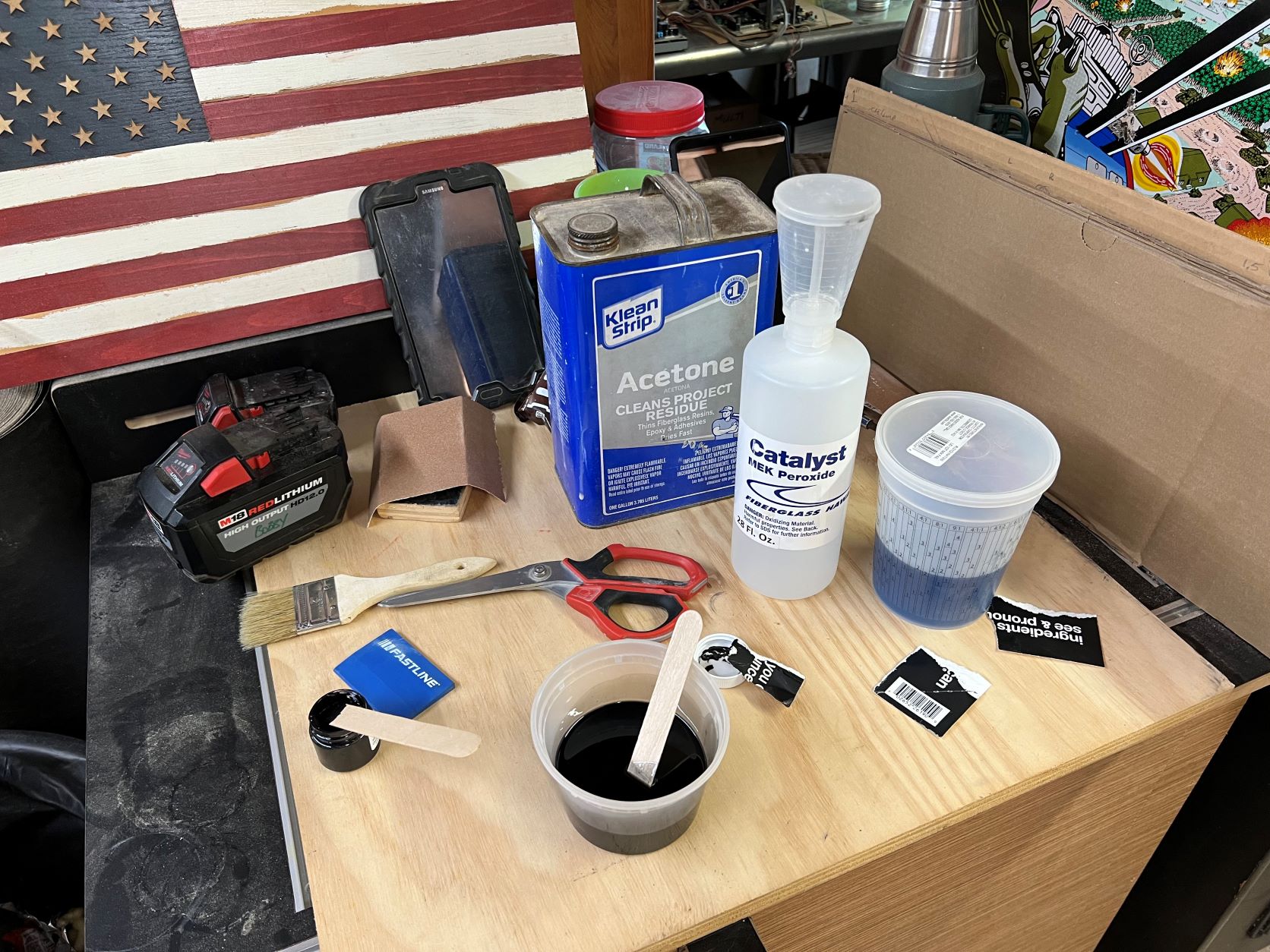
Mix it hot (like a 2% ratio) and let it rip.
It has been hot, humid and disgusting here for a few days (by our standards) so nothing makes the joyous exothermic reaction of resin going off happen quicker.

I figured that the hard angle sweep of part of the bezel would make for not perfect flatness with my cloth- so that I would need to add a step and put on an un-hardened hot coat of resin before I layed down the final layer.
For anyone who may for some reason give a ---steaming pile of meadow muffin---, when you are playing with polyester resins, if you want the stuff to be easy to continue to add layers to without having to sand it first (and thereby physically opening up the ends of those styrene monomer chains for further resin bonding) you use pure resin- that is, something that doesn't have surfacing agent- i.e. wax- added to it.
I did that here because I wanted to get a nice flat layer on my last (3rd) pour of resin so that I only needed to polish it.

That layed pretty flat but still needed some sanding work (as expected) so I gave it a rub with 120 grit to get it to shape and blew the dust off to add another layer of resin.
I used to think that you needed to give any substrate a wipe/wash with acetone to make sure it was contaminant free for subsequent layers- but this actually creates problems.
Blow off any sanding dust or other crap and press on.
For your final coat of resin you WANT to add wax (which isolates the reaction from atmosphere- and closes the ends of those polyester chains) so that your work can be sanded without gumming the crap out of your sandpaper.
As I wanted this to be black through and through I kept adding pigment to every layer.
The final coat actually came out pretty decent.

I'll let this last layer harden overnight at least so that it will sand nicely with 400 and 800.
I want it to have a flat finish or I would continue sanding at least to 1200 before I hit it with compound and a buffer.
We'll see how it looks by the end of tomorrow.