Current status: Playable, nearly complete

This is Project Jetsam, a bartop build using only recycled parts and scrap wood.

It's built around an old Windows 8-era Dell Inspiron All-In-One computer with a dual core Celeron, 4GB RAM, Intel HD graphics, and WD 500GB HDD.

Operating system is Linux Mint 21, with Pegasus Frontend running effectively as the shell.
Control interface is an Xbox360 gamepad hack, and audio is handled using an old set of Logitech X140 desktop speakers and amplifier board. Speakers were decased, with the faceplates and grilles reused to facilitate speaker mounting in the rear dogleg of the cabinet. Joystick and buttons, off-brand IL clones, were salvaged from a Microcenter retail control panel which had been purchased and upgraded a couple of years ago.

The audio amp, i/o ports and internals can be accessed through a service door in the rear. The door pull is one of the thumbsticks from the Xbox 360 controller used for the controls hack.

An old 4-port USB hub with one dodgy port was used for admin i/o (keyboard, mouse, USB thumbsticks, etc). The hub is not visible in above pic but is located directly below the HDD seen in the center. Audio amp board with volume controls is in the lower right.

The control panel and cavity are set up to allow for modular/swappable control panels. The control panel has stanchions matching the angle of the front fascia so that it just drops into place vertically but allows no lateral or longitudinal movement during use. I had considered using locating dowels at the top edge of the panel to secure it, but that seems not to be necessary. A small "safety panel" was added in the lower left to help keep prying fingers away from the area of the cab where AC connections are made.

Xbox controller hack mounted to underside of control panel. It's ugly, but it works. I'd never bother with a pad hack again, and wouldn't have for this one except that I had decided to really lean into the 'recycled parts' nature of this build as it progressed.

This is the loading screen presented to the user as Pegasus frontend loads from boot.
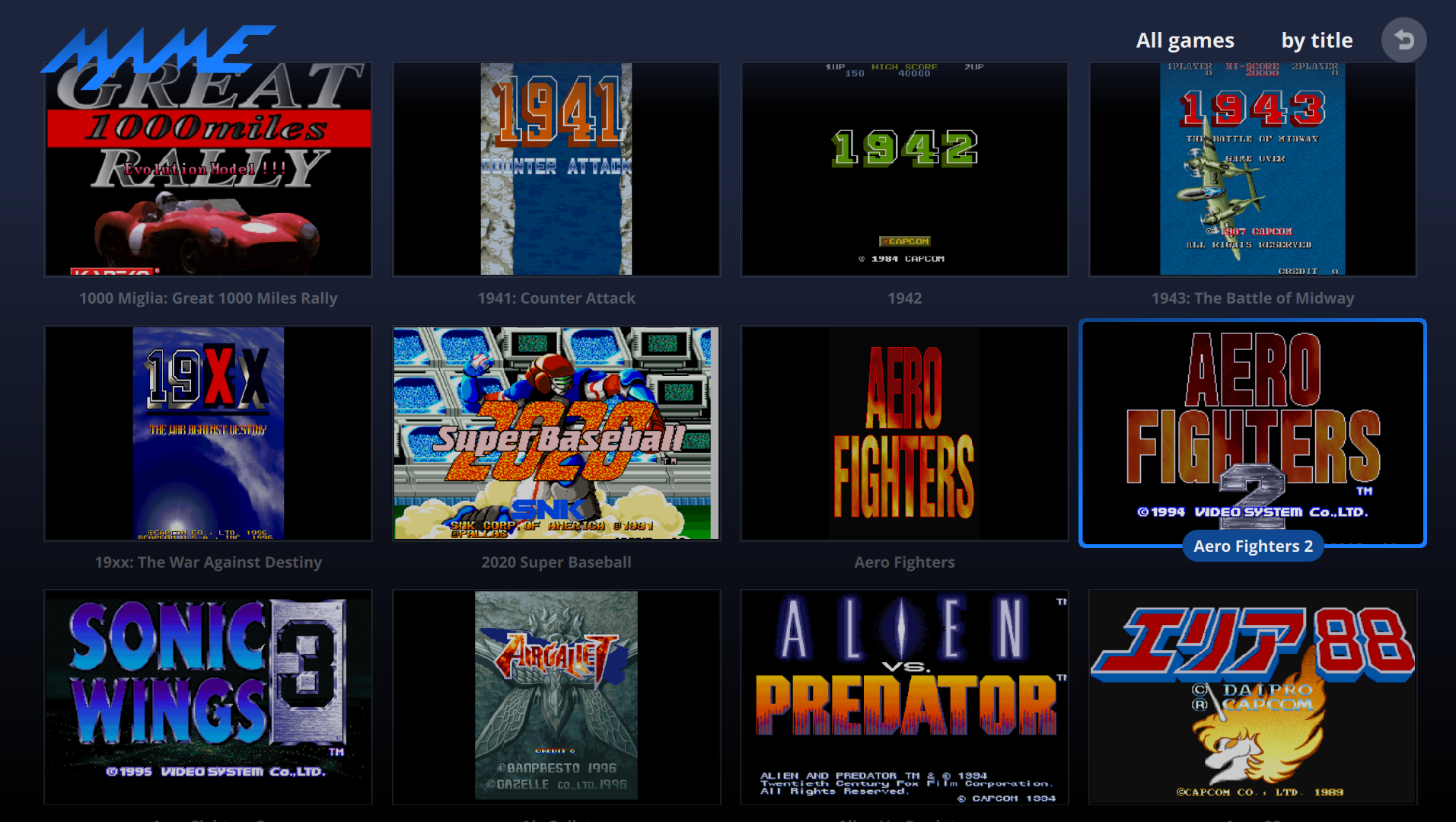
...And this is the game selection interface within the frontend. All UI functions can be controlled using the player controls, including system suspend, restart and shutdown. A single external arcade button mounted to the side of the cabinet is wired to the PC power switch, and puts the system into suspend (sleep) by default.
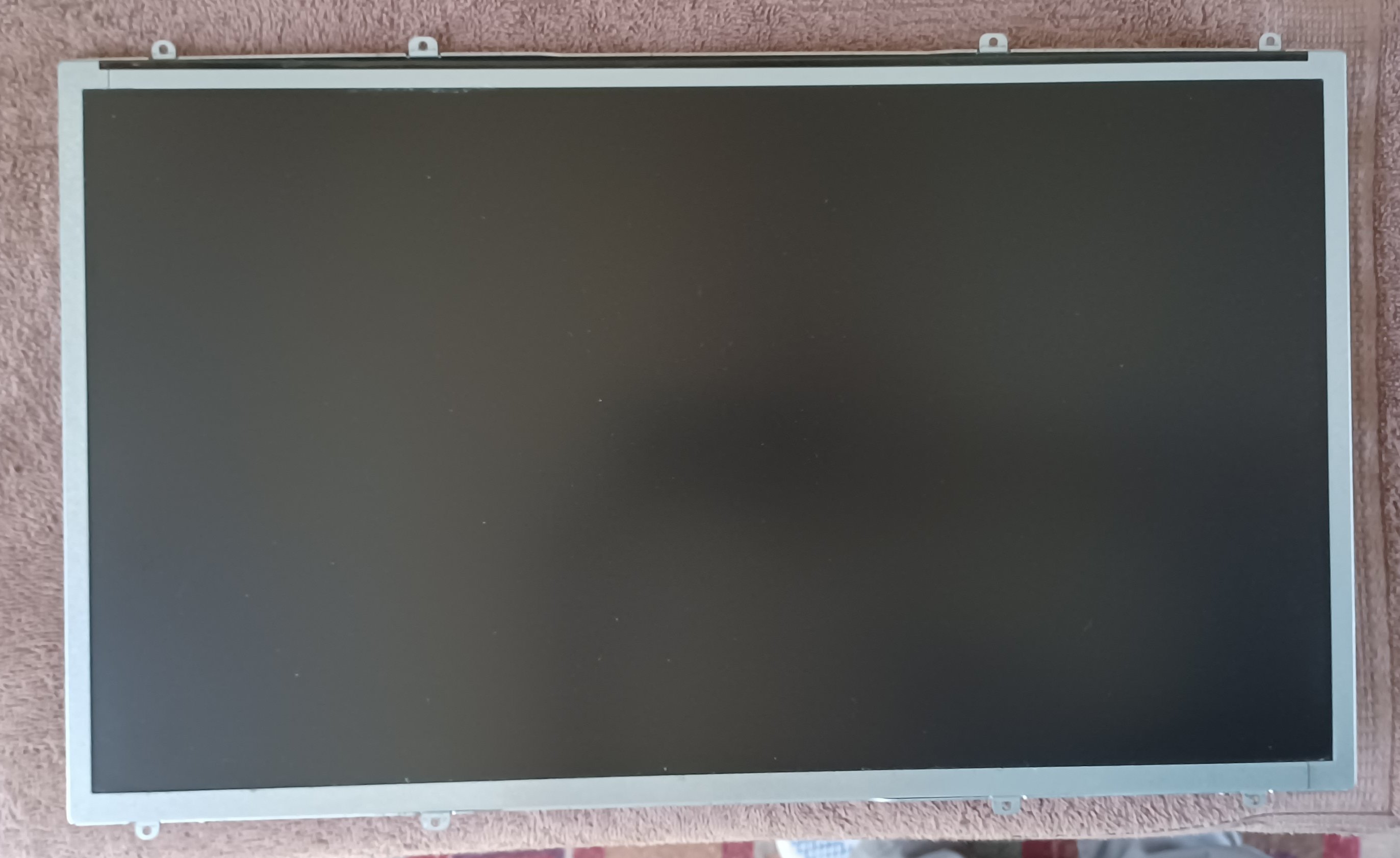
The Dell Inspiron Model 3043 computer with 19" 16:9 LCD. The monitor is marginal with backlight bleed at the bottom edge, and the onboard usb ports were very flaky with intermittent connection. The port headers were reflowed and that seems to have improved their reliability.
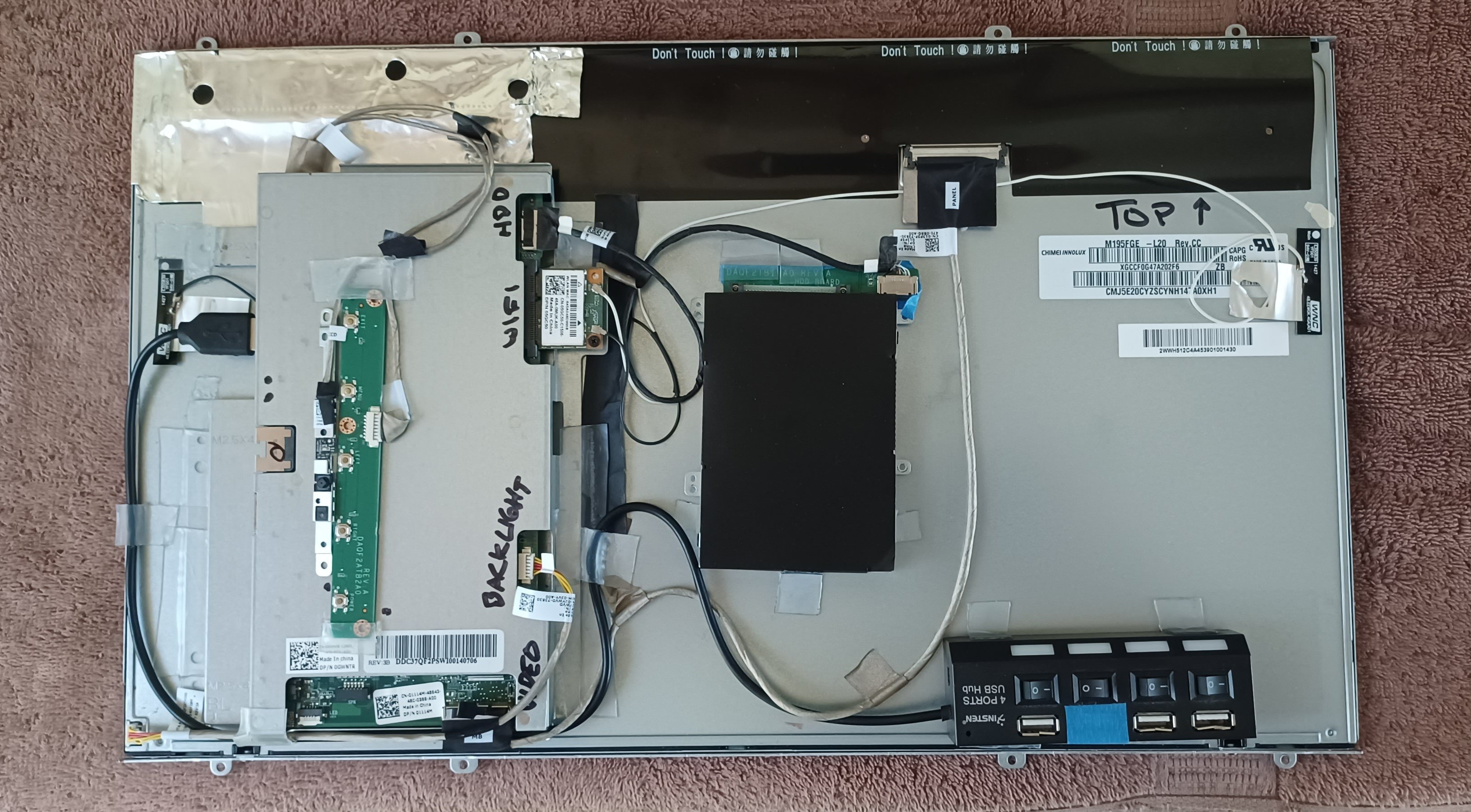
The computer was on its way to e-waste, but I decided that a bartop build might be a fun use of it on its way out. System was decased, and daughterboards + accessories remounted to the rear of the monitor case with hot glue and flex seal (lol). All (DC) electrical connections which needed to be modified are soldered and heat-shrinked.
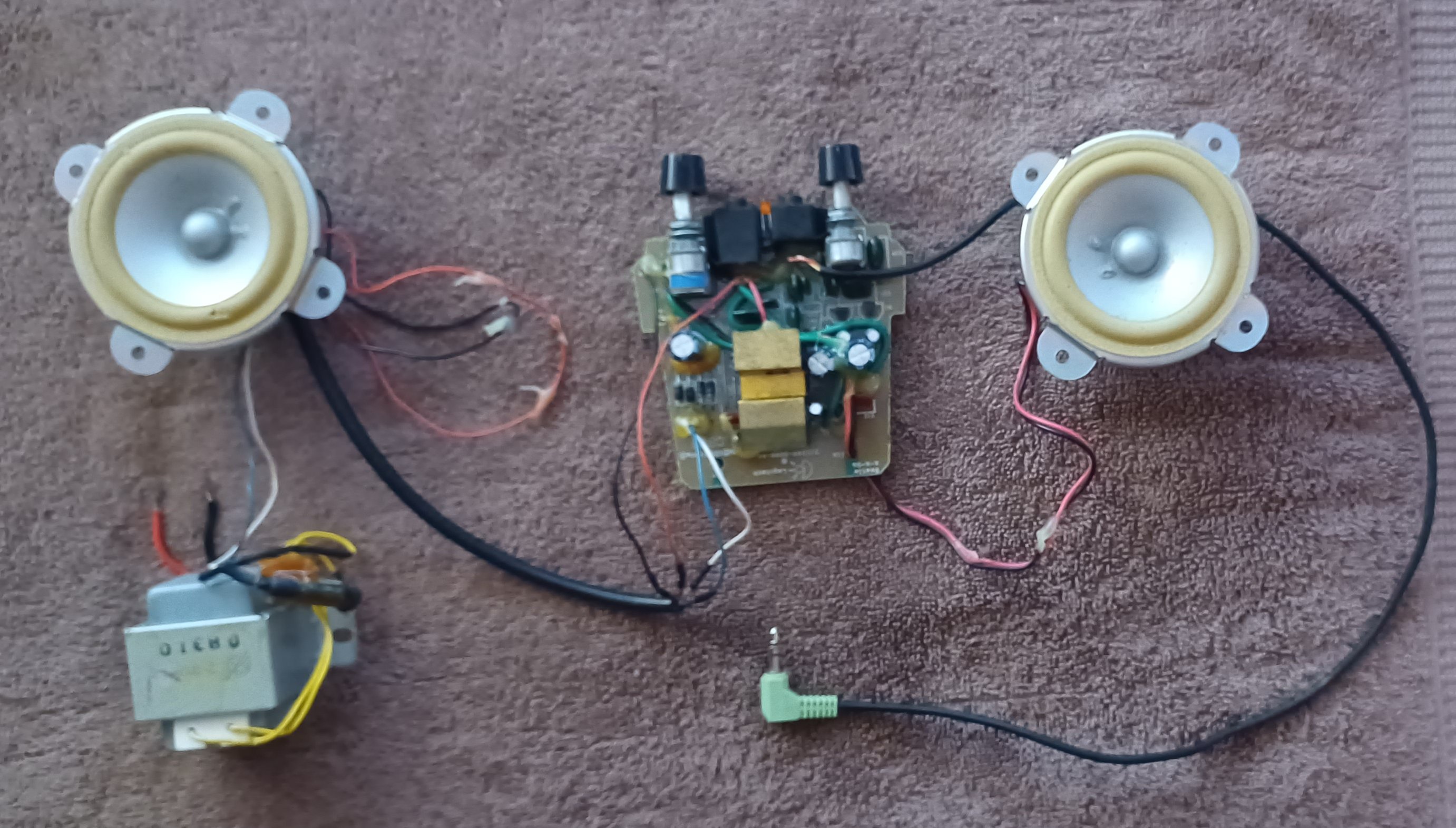
Decased Logitech speaker system. This model uses a 10.6V AC transformer which was mounted into the base of the cabinet and ganged to the AC input for the computer's small power brick. The power switch for the audio amp is part of the rotary volume control, so in combination with the computer's internal monitor shutoff circuitry no relays or smart strips are necessary to power off the machine.
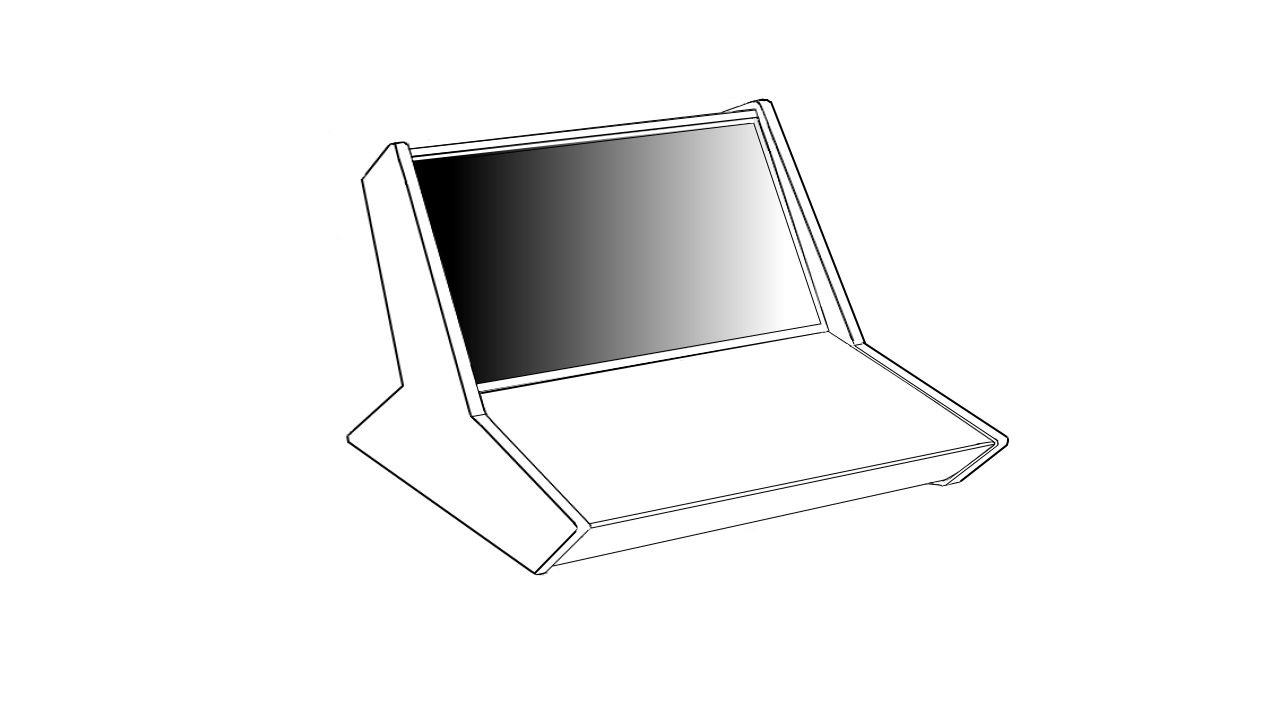
This was the design sketch I came up with to kick off the project. I didn't want to do yet another mini-Taito, mini-Atari or mini-Nintendo bartop, and wanted to make it as slim and compact as possible, 16:9 monitor notwithstanding. I elected to go with a z-back profile with the monitor raked as far back as its limited viewing angle would allow. Likewise I decided against a marquee box, as this machine is not meant to emulate the appearance of any actual arcade cabinet.
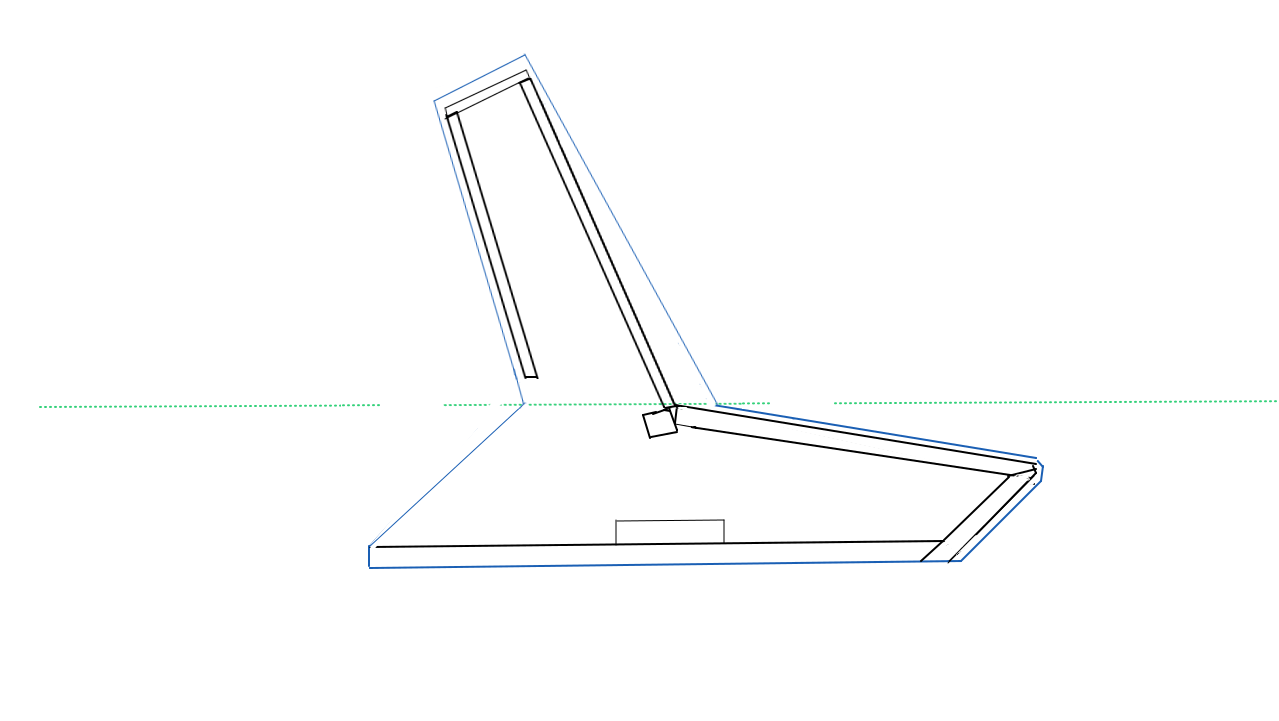
I extrapolated the profile into this rough elevation sketch to help determine the dimensions needed to accommodate the monitor and help visualize where the internal battens could be placed. I decided early on to go for a rear-firing speaker arrangement to be housed in the dogleg at the lower rear.
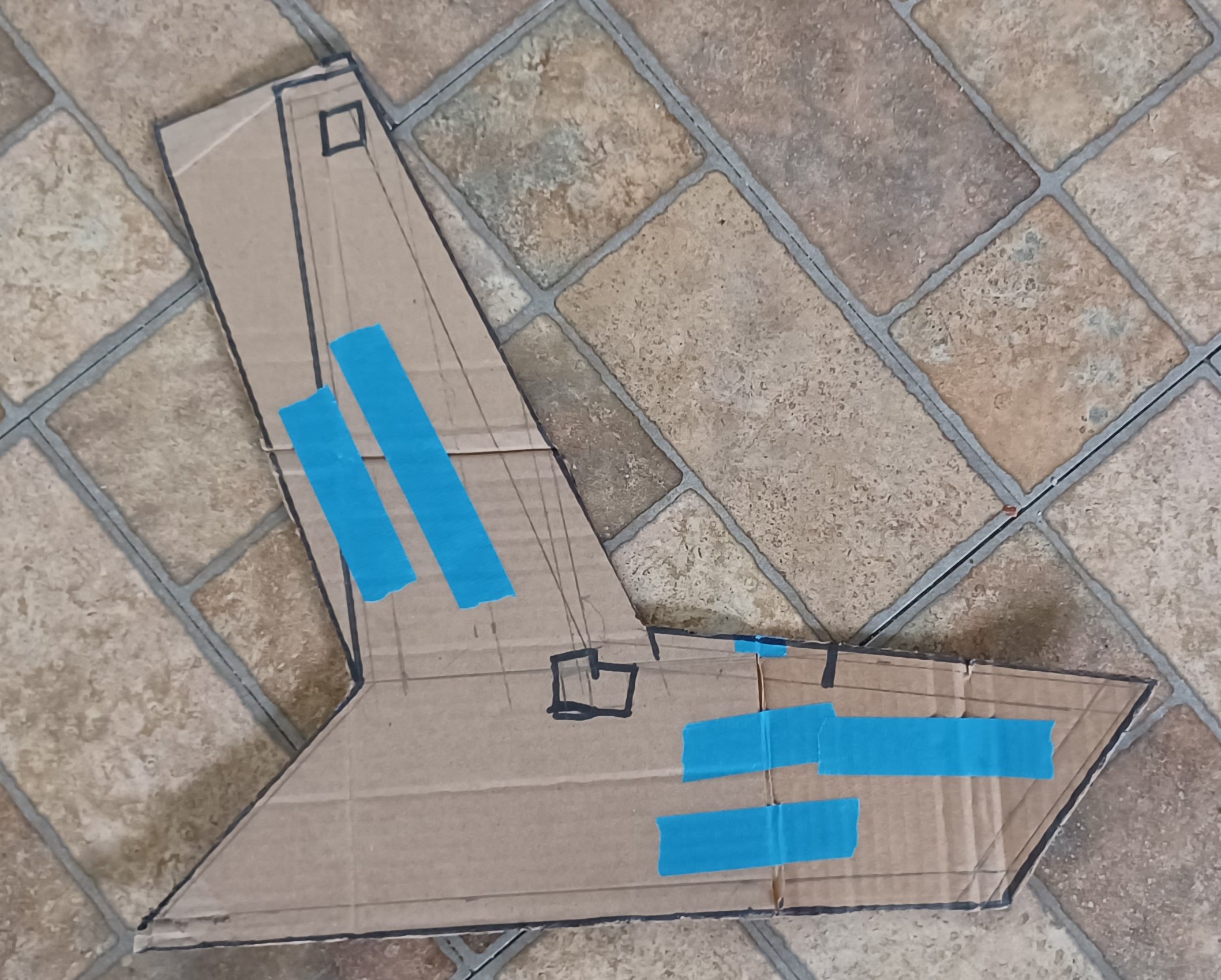
A rough cardboard template was made to establish the shape and I proceeded to make sawdust.
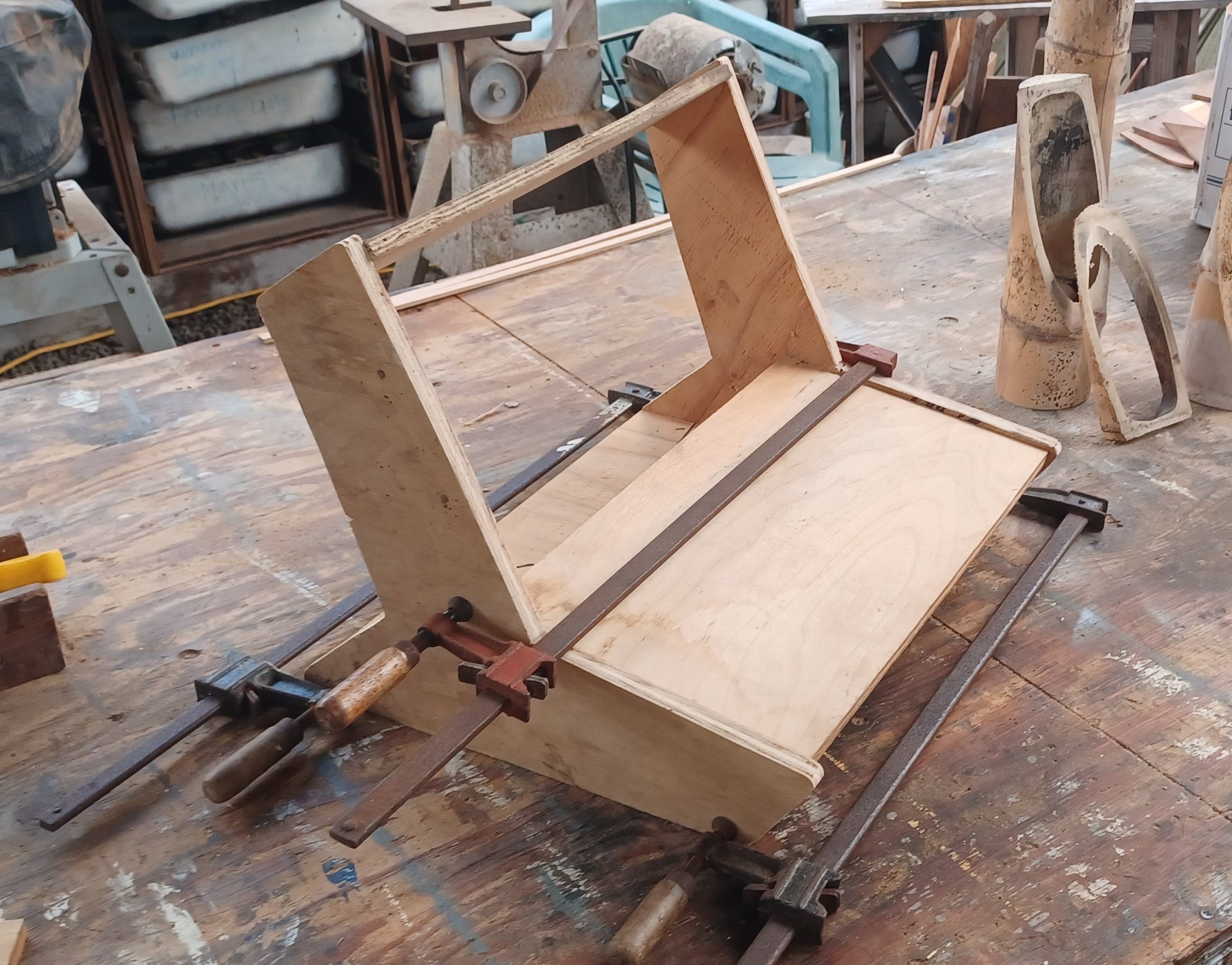
First mockup using wood cuts to check dimensional fit prior to glue up. All of the wood materials used are remnants and offcuts from other projects, but could comfortably be cut from a half sheet of plywood. For this build a variety of 1/2" and 12mm ply was used.
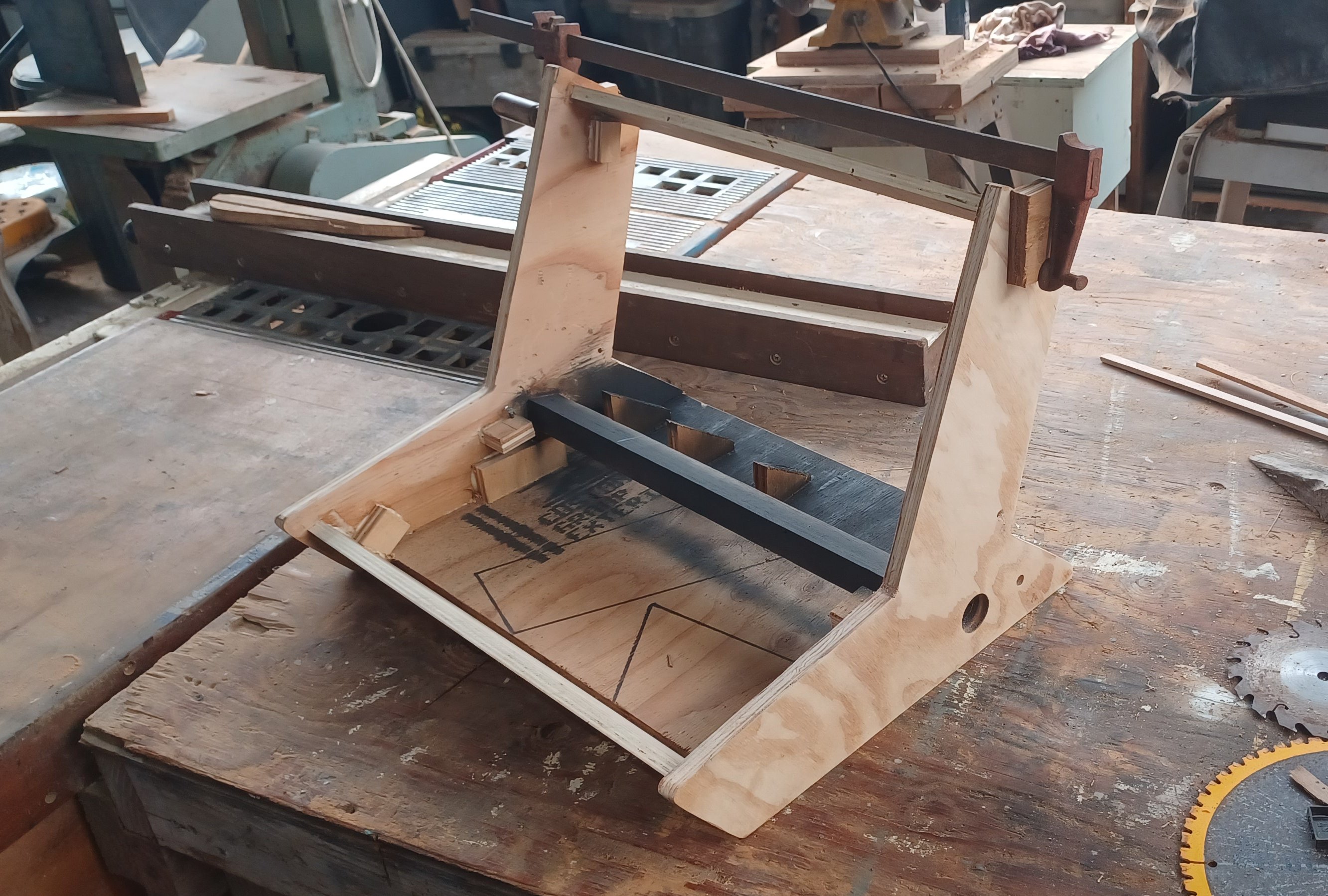
Final glue up of header bar above monitor. Minimal battens cut from ply were used to help preserve space for internal components. Crossbar in the middle is the monitor support, which also carries the audio amp, usb hub, and serves as a separator for the control panel cavity. The large hole in the exterior panel at the right is for the machine's power button, and the smaller hole behind it is the hole for the AC cord strain relief grommet.
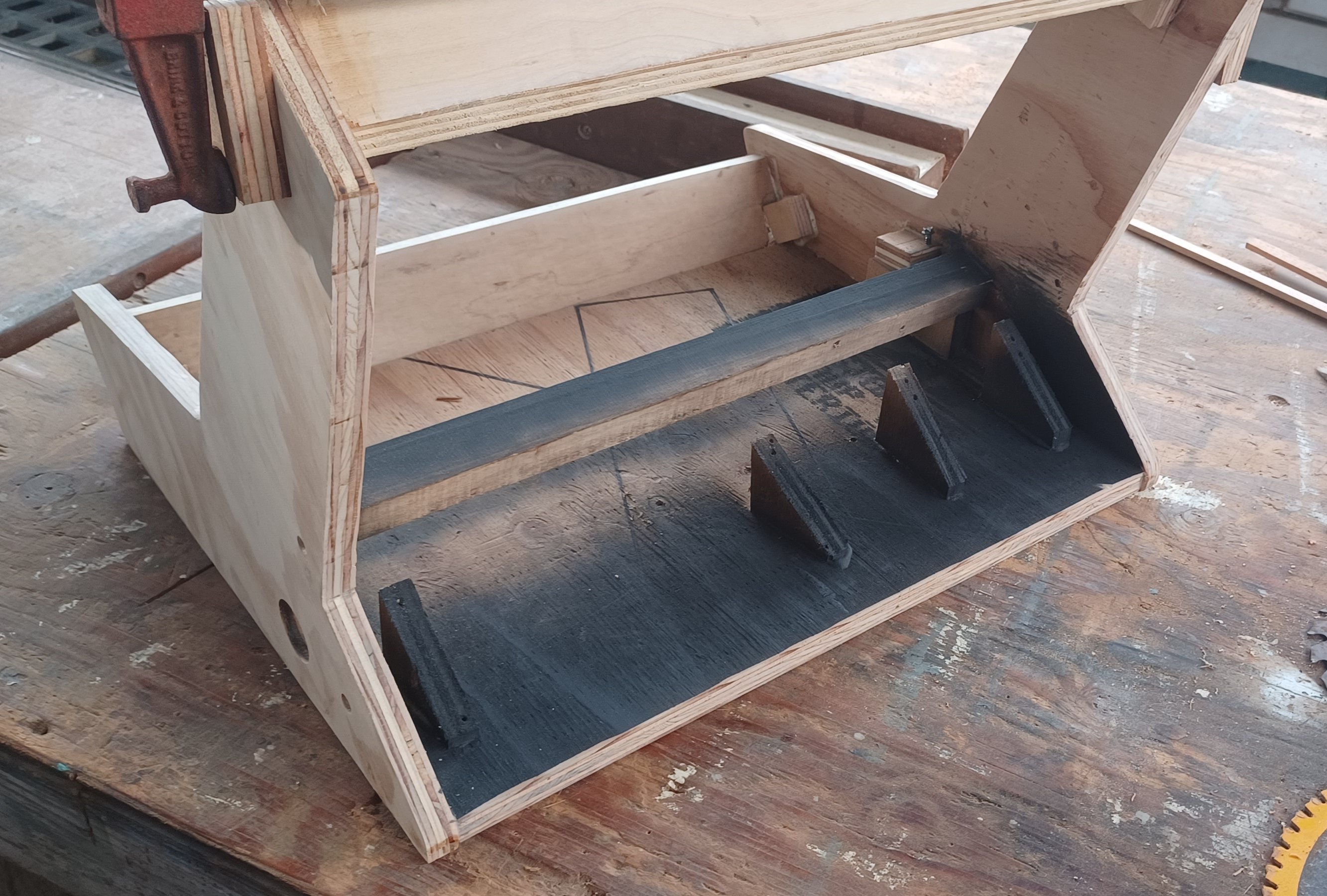
The rough plywood wedges in the dogleg area are mounts for the speaker faceplates which carry the drivers, passive radiators, and speaker grilles.
The next steps will be to determine what sort of deco/finish I want for the unit (I'm leaning toward woodgrain vinyl wrap for the sides), application of 1/2" edge moulding (will be using adhesive countertop edging rather than t-molding), addition of rubber feet to the underside, and addition of acrylic overlays for the monitor and control panel (tolerances were planned in advance to allow for overlays).
Thanks for reading this far. Finishing suggestions are welcome!